High pressure die casting aluminum housing for electrical accessories
Product Details
Processing | Aluminum die cast/die casting/high pressure die casting |
Trimming | |
Deburring | |
Bead blasting | |
Surface polishing | |
CNC machining ,tapping ,turning | |
Degreasing | |
Powder coating with black color | |
Inspection for size | |
Machinery | Die casting machine from 280~1650tons |
CNC Machines 130 sets including brand Brother and LGMazak | |
Drilling machines 6 sets | |
Tapping machines 5 sets | |
Degreasing line | |
Automatic impregnation line | |
Air tightness 8sets | |
Powder coating line | |
Spectrometer (raw material analysis) | |
Coordinate-measuring machine (CMM) | |
X-RAY ray machine to test air hole or porosity | |
Roughness tester | |
Altimeter | |
Salt spray test | |
Application | Aluminum casting base,motor cases, battery cases of electric vehicles, aluminum covers ,gearbox housings etc. |
Applied file format | Pro/E, Auto CAD ,UG, Solid work |
Lead time | 35-60 days for mold , 15-30 days for production |
Main export market | Western Europe,Eastern Europe, USA |
Company advantage | 1) ISO 9001, IATF16949,ISO14000 |
2) Owned die casting and powder coating workshops | |
3) Advanced equipment and excellent R&D Team | |
4) Highly skilled manufacturing process | |
5) A broad variety of ODM&OEM product range | |
6) Strict quality Control System |
Procedures of Die Casting Production:
1. Inquiry- Check all requirements are clear -->
2. Quote based on 2D and 3D drawing-->
3. Purchase Order Released-->
4. Mold design and production issues confirmed--->
5. Mold making-->
6. Part Sampling-->
7. Sample Approved-->
8. Mass production--->
9. Parts delivery--->
DFM Description of ALUMINUM DIE CASTING
Design for Manufacturing (DFM) is a term often used in engineering. It refers to the process of optimizing production to
make it as simple and cost-effective as possible. DFM focuses heavily on the manufacturing methods and processes used.
One of the main advantages of DFM is that it allows problems with the production method to be detected and solved early on
in the design phase. At this stage, issues are much less expensive to resolve than when they are discovered during or after
the production run. Applying DFM techniques allows for a reduction in the costs of manufacturing while maintaining a good or
better standard of quality.
In order to optimize the production process of aluminum die casts, the following objectives should be targeted:
1.Use the least amount of casting material possible,
2.Ensure that the part or product will easily come out of the die,
3.Minimize the solidification time for a casting,
4.Reduce as much as possible the number of secondary operations,
5.Ensure that the final product will perform as required.
Our factory view
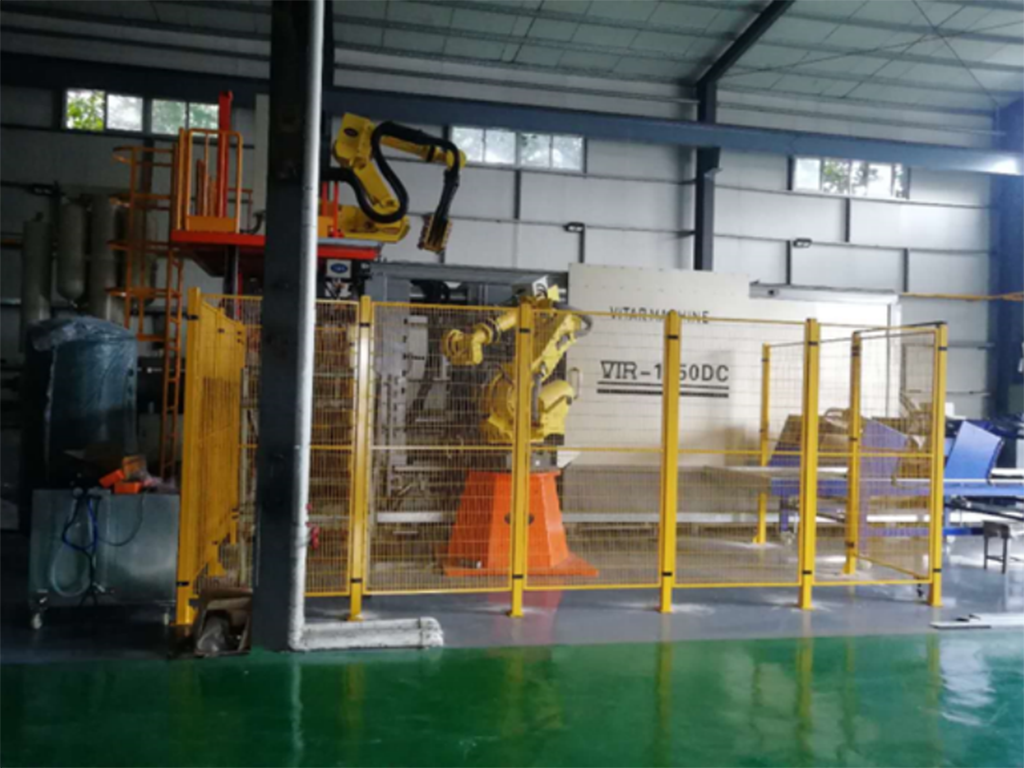

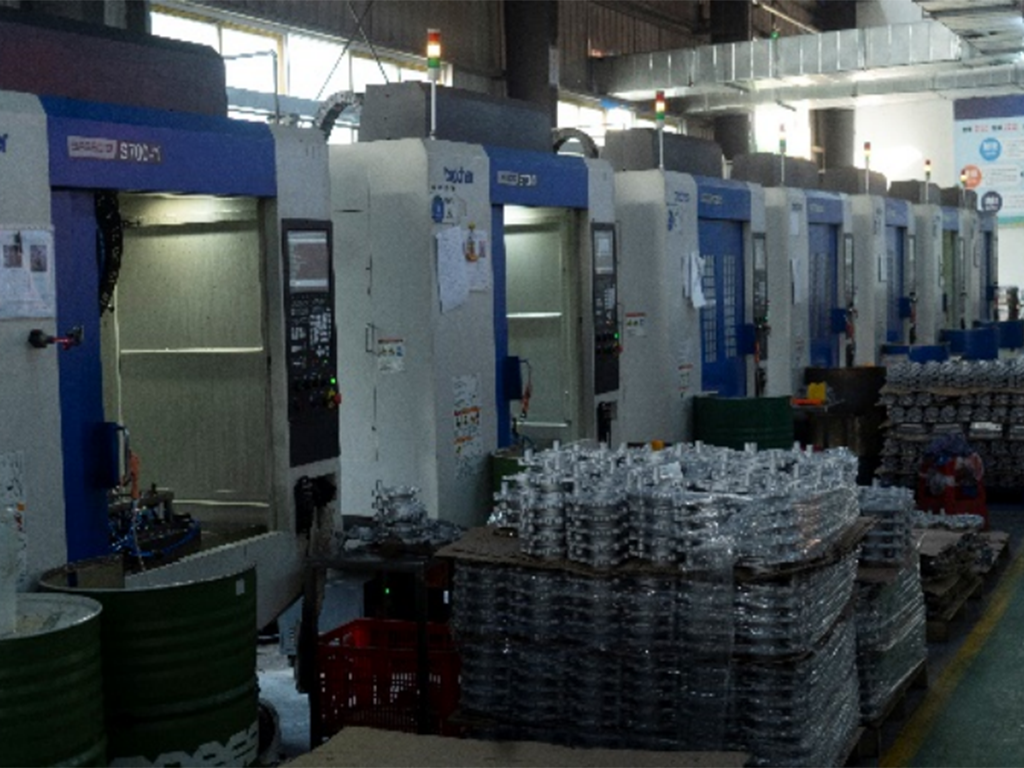
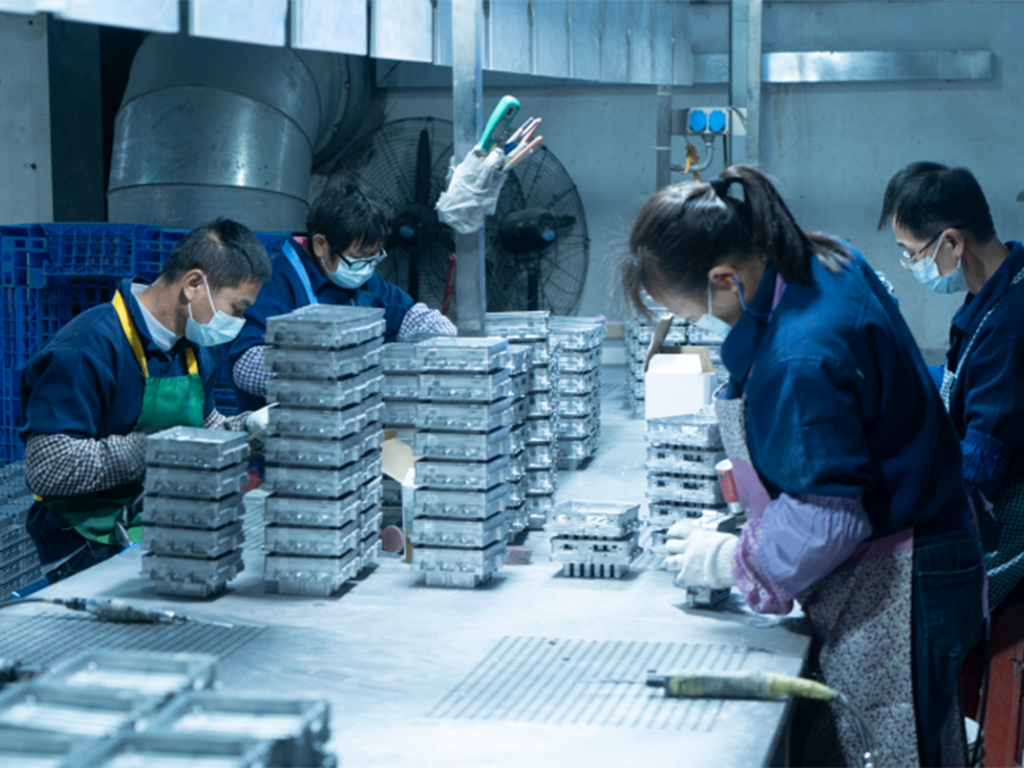
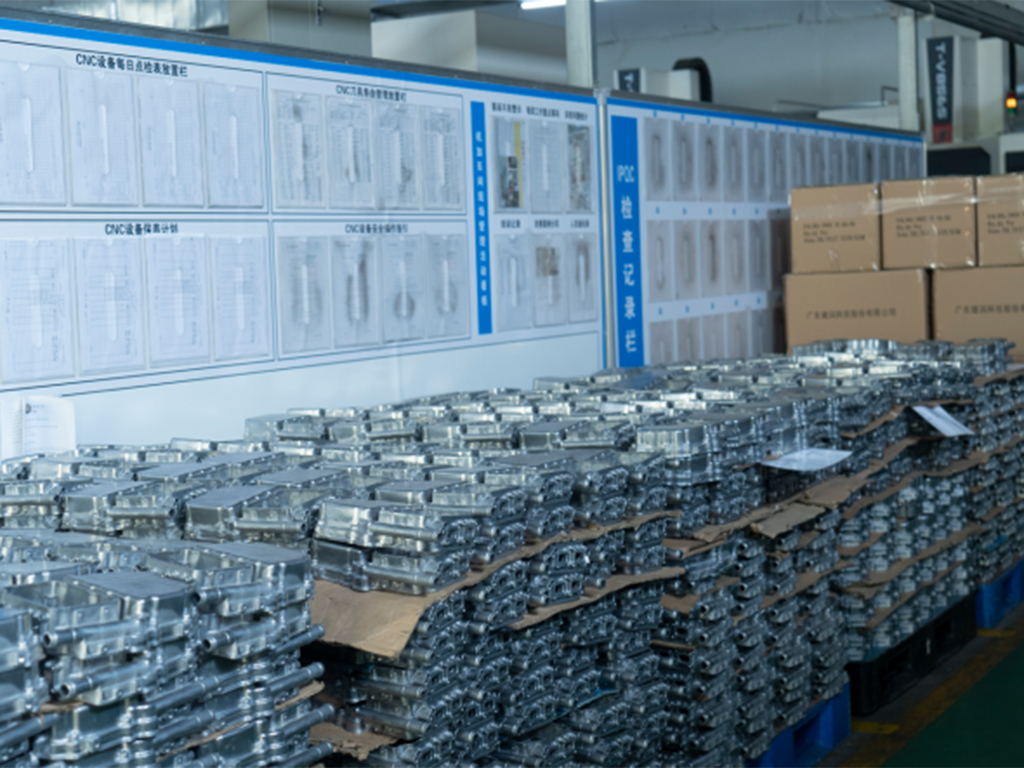
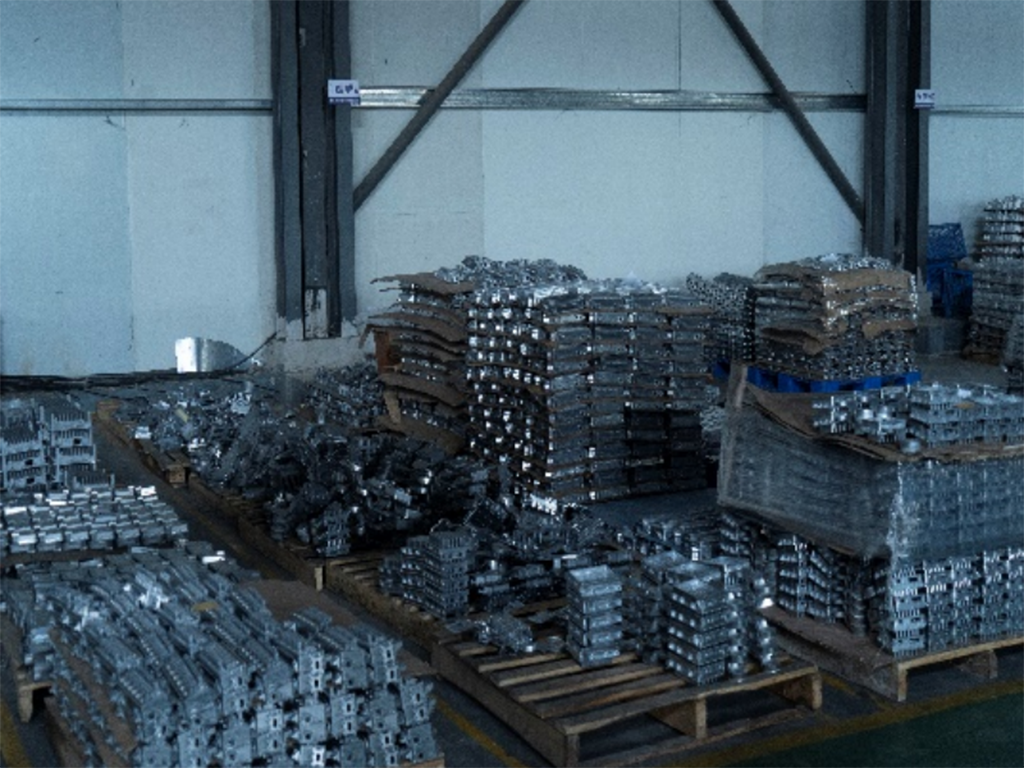
We have full services except above processing ,we do the surface treatment in house including sandblasting ,chorme plating ,powder coating etc . our goal is to be your preferred partner , welcome to send us the inquiry at info@kingruncastings.com
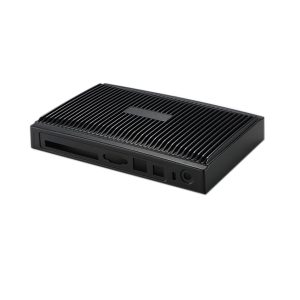
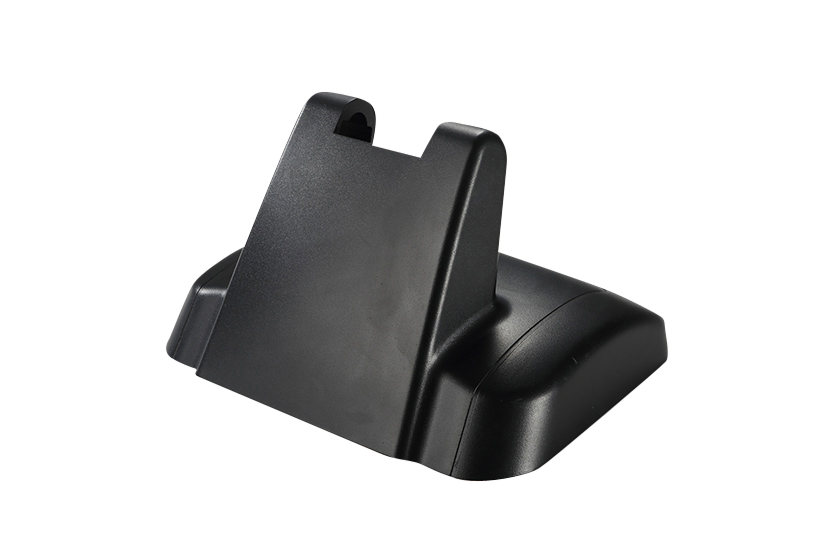